Continued Professional Development (CPD) is an important way to ensure professionals stay up-to-date on best practice and industry knowledge. Life-long learning is paramount to retaining and gaining additional skills and abilities. Looking outside of the constraints of daily routines and learning from others is a valuable experience, often allowing for cutting edge thinking and service design. As such Christina from Heart of London Business Alliance (HOLBA), Laura from Veolia and Jarno from Westminster City Council (WCC) took some time off, away from their respective offices, to join a waste management study tour to Hamburg, Germany. The study tour was organised by the London and Southern Counties Centre of the Chartered Institute of Wastes Management (CIWM).
Germany has long been recognised as a worldwide leader in advanced sustainable waste management and the City of Hamburg in particular is a leader in its field amongst European cities. It is no surprise that they won the European Green Capital Award back in 2011. Hamburg is Germany’s second largest city, after its capital Berlin, and the metropolitan region is home to over 5 million people. It has a long and rich history which includes the period of the Hanseatic League of ports and cities, founded in the late 1100s.
Hamburg is now a major trading port, industrial centre and important junction of several motorways, shipping routes and railways making it an ideal transportation and trading hub. It serves as an international gateway to Scandinavia, and the central and more eastern parts of Europe. It is also home to a vast area of industry ranging from (petro-) chemical complexes and refineries to shipbuilding (Blohm & Voss) and processing of imported goods and resources.
Due to a desire to rank amongst the best in class around environmental management, Hamburg is home to a number of unique environmental operations not found in London. The recent study tour allowed the CIWM group of delegates to see specific waste and environmental management operations and processes up close, allowing them to take best practice home with them. Delegates came from a wide variety of waste professionals ranging from London Boroughs and consultants to airport operators and waste management providers. Some delegates had travelled from as far away as Nigeria to join the study tour. The tour was of particular interest due to several key elements currently proposed in the UK government’s Resources & Waste Strategy (RWS), such as Deposit Return Schemes (DRS), Extended Producer Responsibility (EPR) and Collection Consistency. These elements have been in operation in Hamburg for numerous years. Our visit afforded the group the opportunity to see them in operation and learn from local experience.
Extended Producer Responsibility for packaging waste
Our first visit involved the EPR system for packaging waste. In Germany all producers, importers, distributors and users of packaging materials are required by law to pay 100% of the cost of collecting, managing and recycling/recovering this packaging after it has been used. A similar system is being proposed for the UK. In Germany the EPR fees paid per material vary, based on a number of factors such as behaviour in the automatic sorting process, recyclability, any non-separable components and the ability to be sorted. For lightweight packaging materials consisting of plastics, metal and composite materials (such as beverage cartons, trays, sachets, etc.) a nationwide collection and recycling system, the ‘Duales System Deutschland’ or DSD, was implemented in the early 1990s. The system was introduced due to concerns around ever-increasing levels of packaging waste and ensuring those causing the waste would take full responsibility for it.
In addition to the DSD system, a comprehensive DRS system is in place where consumers take empty drinks packaging back to retailers in order to reclaim their deposits.
The DSD system is funded through the EPR money paid by those legally required to pay into the fund. The system is more popularly known as the ‘yellow bag/bin’. Contracts for the collection and sorting of the ‘yellow bin’ materials are awarded to recyclers by DSD based on operator performance, affordability and sustainability. Contracts are heavily audited and monitored to ensure high performance and compliance with German packaging waste legislation.
In more recent years the City of Hamburg has also allowed certain non-packaging materials, that are similar to packaging materials (plastic buckets, toys, cutlery etc), to be thrown into the yellow bin. These materials can be processed and recycled the same way as the packaging waste.
Veolia Germany operates a large sorting facility in the east of Hamburg where all material collected in the Hamburg region via the ‘yellow bin’ system is sorted for recycling or recovery. A separate collection contract for the yellow bins and bags is held by WERT (translates into ‘Value’) which is an arms-lengths operated subsidiary of the municipal cleansing department SRH (Stadtreinigung Hamburg). The city purchased this, previously privately-operated, company in order to have better control over its waste stream, costs and environmental performance.
At the Veolia sorting facility, we saw first-hand the challenges that such a vast variety of different packaging materials can create. As in the UK, there are issues around contamination i.e. the wrong materials or packaging not being empty, clean and dry being thrown into the recycling. Only the right materials, in the right conditions can be recycled. Everything that is rejected from the process is shredded into a high-caloric fluff-type fuel for cement kilns.
It was noted that recyclability of a number of different plastics and composites are limited, especially now export the Far East has (rightly so) been restricted. The German government recently introduced enhanced packaging waste legislation targeting difficult-to-recycle materials and also to increase the percentage of materials the DSD system recycles to 63% by 2022 (currently 36%). Even in 2022 this would still see nearly 40% of plastic and composite packaging materials being converted into fuel for the cement industry. It is evident that more work needs to go into designing packaging materials that can actually be recycled.
Dealing with extremely hazardous waste
Hamburg is home to a large production and manufacturing base due to its location and large port. It is an important hub for chemical and petrochemical industries, and home to major plants operated by big names such as Bayer, Beiersdorf, BASF, DowDuPont, BP, Pfizer, Shell and Novartis. These industries create substantial volumes of chemical and hazardous wastes requiring bespoke treatment solutions to safely destroy them.
From the mid-1970s onwards, Hamburg realised that simply tipping industrial waste into landfills would create even bigger problems. Exporting it to East-German landfills, behind the Iron Curtain, under the ‘Dreck gegen Devisen’ policy, also led to issues. They found a safe alternative in high-temperature hazardous waste incineration. For many years the plant in the Borsigstrasse, operated by AVG which is part of the Indaver Group, has provided a responsible and sustainable solution for destroying hazardous and special waste types. The plant is one of the biggest of its kind in Europe, treating around 150,000 tonnes of waste per year. Waste is delivered in a variety of forms, from gaseous and liquid to pastes and solids. Each form requires a different handling procedure before combustion. The facility is very flexible in the number of containment options, it can accept waste loose, bagged, in drums, in tankers, in small (consumer) packaging, roll-on roll-off containers and special hazardous waste bins.
Some waste types are so volatile that they cannot be stored until treatment, instead requiring injection into the rotary combustion kiln straight from the tanker truck that delivers them. The heat from the burning waste is captured in the boiler system and sent directly, as steam, to the nearby ‘Tiefstack’ power station which generates electricity as well as heat for Hamburg’s district heating system. The waste the facility treats does not only originate from the Hamburg area. The facility helps out a number of European countries, which lack similar specialist infrastructure, by treating their chemical and hazardous wastes. Some waste has even been sent for destruction from the UK.
Combusting hazardous and chemical waste is a highly specialised skill in order to ensure no toxic or dangerous by-products are produced by the handling and combustion process. The plant has an extensive flue gas cleaning system ensuring it operates within very tight emission limits. Constant monitoring of the treatment process ensures these limits are not breached. The plant strives to be an environmentally responsible role model. The skill and expertise of on-site staff were exemplary and provided the group of delegates with a unique learning experience of this bespoke and often overlooked aspect of waste treatment technology.
Stadtreinigung Hamburg’s municipal waste management
Hamburg’s municipal organisation is very different to London’s. Whilst the city has boroughs (‘bezirke’), these do not hold the autonomy and self-governance associated with London Boroughs. Hamburg operates as a single city as opposed to London’s cluster of cities set-up. Waste and recycling collections for residents and businesses are centrally provided through Stadtreinigung Hamburg (translates into City Cleansing Hamburg) or SRH for short. Like Westminster City Council, SRH works with low emission trucks and is also working on implementing a fully electrically operated collection fleet. Great minds think alike.
At present Hamburg recycles around 40% of its municipally managed waste which is increasing year-on-year as part of an ambitious programme to recycle more. Waste is segregated by residents into 5 main streams (glass, paper/cardboard, light packaging, organic waste and general waste) of which 4 are collected door-to-door. Glass is not collected door-to-door but instead is recycled through a large number of publicly accessible glass container sites (‘bottle banks’). A number of other ad hoc waste types such as electrical appliances, hazardous waste, textiles and rubble can be dropped off at the household waste recycling centres (HWRC) run by SRH.
Businesses are legally obliged to segregate their waste into 8 streams (paper & cardboard, glass, plastics, metals, wood, textiles, organic / food waste and general waste) provided these are being produced. Hamburg’s businesses manage to segregate their waste into the associated fractions despite some being based in a historic, dense and busy city centre with old buildings. A quick and dirty solution like the UK’s dry mixed recycling set-up is not allowed (nor needed) in Hamburg.
Most waste streams are collected containerised with the size of receptacles ranging from 120 to 1100 litres. The bins are placed on the pavement by the waste producer or building manager so they can be collected. In a small area of the historic inner-city special plastic bags are still being used, similar to bags used in Westminster, however the City of Hamburg has made great progress over the past few years to phase out these sometimes-troublesome plastic bags. Instead they are moving to a centralised collection system which keeps their streets clear of waste bags.
A number of properties have waste bins collected straight from internal storage areas or basements. The collection crews hold special keys and access codes to access these buildings. Where SRH, or its subsidiary WERT, have to collect bins from inside the property, a special handling charge is levied to cover the additional cost of service provision. Having witnessed first-hand how Hamburg’s street scene avoids being burdened by waste as London’s can be, various proposals to reduce the impact of waste bags on Westminster’s streets will be evaluated.
SRH operates an extensive collection service for mixed food and garden waste (bio- waste). Whereas in the UK this particular material can only be sent to lower-performing in-vessel composting (IVC) facilities, in Hamburg bio-waste is sent to a specially adapted version of anaerobic digestion (AD), undergoing a so-called dry-AD process. Overall, AD is the better performing treatment option for bio-waste since the process generates energy (biogas), rather than being a user of energy (as IVC is).
In the UK, the wet-AD process is extensively used to treat food waste. Wet-AD is reliant on pulping the waste first, then mixing it with water into a slurry which can then be digested. Wet-AD cannot treat garden waste since it does not pulp properly. As such the UK has seen the rise of segregated food waste and garden waste collections over the past 5 years. Synergies can be made when collecting bio-waste (vehicle movement reduction, reduced operational costs etc) however this is reliant on the dry-AD process to treat the material, which is not currently the case (yet) in the UK.
The dry-AD process is also more cost effective compared to IVC, which results in lower tipping fees. The dry-AD process is more tolerant in what it can accept for treatment, compared to IVC and wet-AD, making it an ideal process for bio-waste. Like wet-AD, dry-AD also generates valuable methane gas during the digestion process. This gas is captured for further use. In Hamburg the gas is refined to natural gas quality and injected into the local distribution grid.
The resulting output from the dry-AD plant after it comes out of the digester is sieved and refined to make a valuable compost. The compost produced in Hamburg is a sought-after product by local farmers, gardeners and horticulturalists.
Compostable packaging creates issues for dry-AD as well since these items do not fully break down in the process, as shown in the photo. UK dry-AD is sometimes heralded as thé treatment solution to the current problem around compostable packaging which contaminates food waste collections and cannot be broken down properly by both IVC and wet-AD. Extensive testing by SRH on a number of compostable materials and using extended treatment periods of up to 10 weeks show that these products still remain largely intact. The group witnessed first-hand how so-called compostable cups, plates and bags came out of the composting process, intact, as reject material since they did not break down as promised by their producers. SRH also has concerns around the plasticisers and chemicals in compostable materials which have been detected leaching into the compost during the treatment process. There are risks around contaminating the land the compost would be applied to in this way, often land which is used to grow food for humans or animals.
Recovering energy from general waste
Hamburg remains a realistic city and understands that no matter how much it recycles there will always be a waste element left that cannot or should not be recycled. They are also very conscious that on top of this, all recycling sorting and treatment processes generate waste in the form of rejects and residues, all of which require disposal. The problems associated with sending waste to landfill were evident in Hamburg very early on, and this led to it being the second city in the world, after Nottingham, to start burning waste for energy production on an industrial scale. The first plant in Hamburg opened in 1896 and put an end to the bad cholera epidemic at the time. Waste would no longer accumulate in open dumps, which encouraged diseases, but instead was destroyed by combusting it. Hamburg as such is one of the innovative frontier cities that deployed energy from waste (EFW) technology.
Much has changed since then and the current MVB energy recovery facility (ERF), next door to AVG in the Borsigstrasse, is the 4th generation plant commissioned and built by the city. The ERF went into operation in 1994, replacing an older plant from the 1960s. It is one of 3 ERFs serving the needs of Hamburg and the surrounding metropolitan area. What makes these ERFs special is their high energetic efficiency since they feed the heat created by the combustion process into Hamburg’s extensive district heating system which covers the whole city. This system of underground pipes distributes hot water to homes and businesses. Hamburg is a city powered by its own waste which avoids the need to burn fossil fuels such as coal, oil and gas. Similar schemes are developed in London however not on such scale. Introduction of these systems to replace natural gas fired boilers will help reduce air pollution from nitrogen oxide (NOx) emissions. Some of the steam generated at MVB is used to run a turbine on-site and generates electricity. This electricity is used to run the plant and export whatever the plant does not require itself to the electricity grid.
Ash left after combustion has all the metals removed for recycling and the inert part of the ash is used as an aggregate in the construction industry.
Another part of the ERF contains a special ( so called ‘fluidised bed’) furnace to use low quality wood waste such as railway sleepers, wood from construction and demolition and chemically treated wood as fuel to generate heat and power. This special furnace contains a whirlpool of sand due to air being pushed through the bed of sand in the furnace. This particular furnace type is ideal to burn biomass fuels such as wood waste. The heat from the combustion process is fed into the turbine to generate electricity and supply heat to the municipal district heating grid.
METHA – dealing with dangerous legacy pollution
Hamburg’s port is located 100 km inland from the North Sea on the River Elbe. It is the 3rd largest in Europe and serves as a gateway to Scandinavia, and eastern and central Europe. Hamburg is the world’s main trading port for coffee beans. Hamburg is also a major port for cruise ships. The navigable River Elbe has many tributaries, which stretch more than 1000 kilometres into central Europe and connects to large population centres such as Berlin and Prague. The Elbe’s watershed (or drainage basin) contains many large current and former mining and industrial areas, a good number of them located behind what was once the Iron Curtain. A large volume of hazardous pollutants such as heavy metals were discharged into the river during times when environmental regulation was lax or simply did not exist. The Elbe carried all these pollutants into the port of Hamburg where the sediments they stuck to settled in parts of the harbour as the river water velocity decreased.
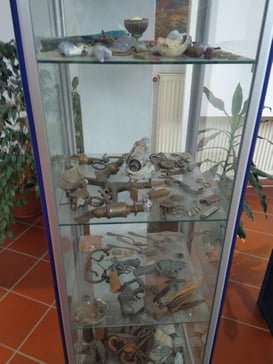
A remarkable feature of METHA is that it is a haven for archaeologists since the dredged sediments often contain artefacts, some of which are on display at the facility.
The resulting sediment accumulations have to be dredged away in order to keep the port navigable for ships, the size of which is ever increasing. The dredged sediment proved a major issue to dispose of since some was too polluted to be tipped into the North Sea. A solution had to be found and in 1987 the Hamburg Port Authority (HPA) developed a ground-breaking treatment facility to segregate pollutants from harbour sediments. HPA describes the facility as ‘the port of Hamburg’s washing machine’. Their research showed that heavy metals mainly stick to finer particles in sediment. This led to a bespoke process being developed to segregate these small particles from other larger particles. Through this process the METHA sediment treatment facility was born. Until recently, when a comparable facility opened in the port of Antwerp, METHA was the only facility of its kind in the world. METHA segregates harbour dredgings into a number of different aggregates such as gravel, pebbles/rocks, fine and coarse sand which then are reused as construction materials. This avoids having to extract virgin equivalents instead. The residual fine sediment fraction, that contains heavy metals, is sent for secure burial on-site in a specially adapted landfill site. Initially, back in 1987, it was thought that levels of heavy metals in harbour sediment would decrease over time to such an extent that in 20 years METHA would be obsolete. Unfortunately, new loads of heavy metals and hazardous legacy pollutants are still deposited in the port of Hamburg. HPA is actually preparing for an increase since, due to climate change, the flow levels of the Elbe have decreased by half. Due to the decreased flow rates, more sediments settle in the port of Hamburg. Another factor affecting the quality of harbour sediment is the increased settling of substances such as micro-plastics, drugs by-products, hormones, pesticide and medication residues since waste water treatment processes cannot remove these completely before treated waste water is discharged in the Elbe watershed.
Our study tour showed that whilst great improvements have been made in the last 30 years around preserving our environment, a lot more remains to be done. Households and, even more importantly, businesses play a key role in establishing a more sustainable way of living for us and future generations. Commercial Waste Services can help businesses become more sustainable and environmentally friendly. Contact us now to discuss.